Tips to Manage Safety in Non-Complex Organizations Using Safety Software
During the summer 2013 aviation safety management software course put on by SMS Pro, a European student brought this Self-Assessment for
Non-Complex Organizations. He was concerned about an upcoming audit. He asked
how SMS Pro could help their flight operations pass this audit.
Consequently, we took an hour from the class and answered each item as follows.
Consequently, we took an hour from the class and answered each item as follows.
Guidance Ref
|
Compliance Y/ N / Partial |
Comments / Reference to compliance | ||
Management commitment and responsibility | 5.1 | Is there a written safety policy endorsed by the Accountable Manager? | Available in Policies & Procedures module. Also notifies when policy requires review. | |
5.1 | Does Senior Management continuously promote and demonstrate its commitment to the safety policy? | CEO commitment visible to all when users come to Safety Workspace | ||
5.1 | Has the safety policy been communicated effectively throughout the organisation? | Safety Policy is visible to all in Policies & Procedures module. Users also review Safety Policy when inducted into SMS Pro. | ||
5.1 | Does the safety policy cover the points in this guidance material? | Left to operator to structure policy. Safety Policy templates available by SMS Pro. | ||
Safety accountabilities | 5.2 | Are the safety accountabilities and responsibilities of the Accountable Manager and other key staff members clearly defined and published for all staff and contractors to see? | Duties & Requirements of Key Safety Personnel module satisfies this nicely. | |
5.2 | Does the Accountable Manager have full responsibility for the SMS and authority to make decisions regarding the budget? | Left to operator | ||
5.2 | Has the management structure of the organisation been defined? | Organization Chart visible to all employees under Safety Policy menu. | ||
5.2 | Are all staff members aware of their safety roles and responsibilities? | Duties & Requirements of Key Safety Personnel module satisfies this nicely. Lists each role and their responsibility. Must review as part of the SMS induction process. | ||
Appointment of key safety staff members |
5.3 | Has a focal point/Safety Manager for the SMS been appointed? | Left to operator. Safety manager information visible to all in Safety Workspace. | |
5.3 | Is there a direct reporting line between the SMS focal point/ Safety Manager and the Accountable Manager? | Left to operator | ||
5.3 | Does the SMS focal point/ Safety Manager have the appropriate SMS knowledge and understanding? | Left to operator. Training is offered by SMS Pro. | ||
5.3 | Does the organisation have a Safety Committee? | Left to operator | ||
5.3 | Does the Safety Committee monitor the safety performance and the effectiveness of the SMS? | Safety committee can monitor the SMS program using Meeting Manager to review issue and document remarks. | ||
5.3 | Does the Safety Committee meet regularly and are the meetings minuted? | Meeting Manager schedules meetings and tracks meeting minutes. PDF archives document meetings. | ||
Emergency response planning | 5.4 | Has an emergency response plan been developed and is it kept up to date? | Left to operator. ERP documentation is stored in version-controlled document manager. | |
5.4 | Are the roles, responsibilities and actions of key staff members defined in the ERP? | These roles & responsibilities can be documented in Duties & Requirements of Key Safety Personnel | ||
5.4 | Does the ERP include all the considerations in this guidance material if appropriate? | Left to operator | ||
5.4 | Is the ERP regularly reviewed and tested? | New emergency drills module helps satisfy this requirement. | ||
Safety documentation | 5.5 | Does the safety management manual or safety documentation in existing manuals contain all the elements as detailed in this guidance material? | SMS Manual Creator has templates of appropriate Safety Manuals. Manuals can be stored in version-controlled document manager. | |
5.5 | Is it regularly reviewed? | Policy for regularly reviewing safety manager can be kept in Policies & Procedures, which automatically reminds user to review Safety Manual. | ||
5.5 | Is there a system for the recording and storage of SMS documentation and records i.e. hazard logs, risk assessments, safety reports from staff/contractors and safety cases? | Issue Manager addresses everything except safety cases. Safety Case Manager holds all the safety cases. | ||
Hazard identification | 6.2 | Is there a confidential safety reporting system? | Issue reporting allows for anonymous and confidential reporting. | |
6.2 | Are safety reports assigned an ‘owner’ and reviewed by the Safety Committee? | Safety reports are automatically assigned a responsible manager who then reviews the report and forwards report to appropriate dept head. Review by safety committee is performed using Meeting Manager. | ||
6.2 | Is there feedback to the reporter? | Automatic feedback occurs when users report issues. They can track progress in multiple ways. | ||
6.3 | Is there a written procedure describing how hazards are identified? | Hazard Identification procedures are stored in Policies & Procedures module | ||
6.3 | Have the major hazards associated with the organisation been identified? | Proactive Hazard Analysis Tool (PHAT) and Hazard Register are used to manage this requirement. | ||
Risk assessment and mitigation | 6.4 | Is there a risk assessment process in place? | Assessment tab in Issue Manager provides a logical process | |
6.4 | Is the risk tolerability matrix appropriate and can it be applied consistently? | Configurable risk matrix can be adapted to all organizations | ||
6.4 | Is there a process for deciding any necessary risk mitigation? | Based on assessment, corrective actions are assigned and tracked as necessary | ||
6.4 | Are risk mitigations and controls being verified/audited to confirm the effectiveness? | Issue Validation module alerts managers when issues and associated corrective actions must be reviewed. | ||
6.7 | Are risks being managed to a reasonable level? | Left to operator | ||
6.9 | Are the hazards and risks recorded on a hazard log? | Hazard log is part of Hazard Registry module | ||
Safety performance monitoring | 7.2 | Have safety performance indicators been defined? | Easily setup and monitored on the Classify tab in Issue Manager. Tracked in various reports modules. | |
7.3 | Are the safety performance indicators reviewed regularly to identify any trends? | Automated trend alerts notify management of developing trends. | ||
Management of change | 7.4 | Is there a process to proactively identify hazards and to mitigate risks when significant changes in the organisation occur? | Management of Change module provides a structured process to manage this task. | |
Incident management | 7.5 | Are safety investigations carried out after incidents or accidents to establish root cause? | Very robust investigation module with root cause analysis, human factors and final report generation exportable to Lessons Learned Library or as PDF | |
7.5 | Are the hazards identified from safety investigations addressed and communicated to the rest of the organisation? | Lessons Learned are generated on the Investigation tab. Lessons Learned can be emailed to everyone in a particular division. | ||
Continuous improvement | 7.6 | Is continuous improvement in the safety performance being achieved? | The routine (annual) gap analysis demonstrates continuous improvement | |
Safety auditing | 7.7 | Are safety audits and surveys carried out? | Audit checklist creator, audit scheduler and audit manager make up the audit suite. Finding and concerns are driven to the risk management framework where corrective actions are tracked. Safety Survey module manages surveys. | |
7.7 | Is there an independent quality system or third party agency that audits the SMS? | Left to operator | ||
Safety training | 8.1 | Have all staff been appropriately trained in respect of the SMS and their safety roles and responsibilities? | SMS Induction Manager documents SMS initial training. Workflow ensures users are trained before gaining access to the program. | |
Communication | 8.2 | Does safety related information get communicated to all staff members as appropriate? | Newsletters and Message Board communicates safety issues to employees. | |
8.2 | Does relevant safety information reach external users/customers etc? | Issue Manager allows emailing notifications to civil aviation authorities and others. Vendor Message Acknowledgement has features to communicate to contractors | ||
SMS implementation | 9.1 | Has a gap analysis been carried out? | Gap analysis module with many models to choose from | |
9.2 | Is there an SMS implementation plan? | SMS Implementation plan lists and documents the progress of each activity. | ||
9.2 | Does the implementation plan reflect the gap analysis? | Implementation Plan Manager is configurable by operator to reflect gap analysis performance | ||
9.2 | Is the implementation plan on target? | Left to operator |
How to best help your
Aviation Safety Management System
Become an SMS PRO
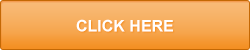
About NWDS - founded in 2003 by six software engineers, NorthWest Data Solutions (NWDS) provides custom computer programming and systems design services. NWDS creates many types of software, including e-commerce, financial, defense, engineering, logistics, aviation and more. In 2007, NWDS developed SMS Pro™ a web based SMS application that supports an organization's overall SMS through safety reporting, safety documentation, safety risk management and safety assurance. SMS Pro™ is currently used by aviation organizations in the U.S., Canada, Asia, Latin America, Africa and the Middle East to help manage their SMS programs. NWDS continues to support SMS Pro™ and add new functionality. NWDS offers custom contract programming services in the U.S. and Canada and is managed by Chris Howell, one of the founders. Their headquarters is in Anchorage, Alaska. For information on NWDS visit their website at www.nwds-ak.com and www.asms-pro.com to learn more about SMS Pro™.